AgroTerra expands the possibilities of its own elevators
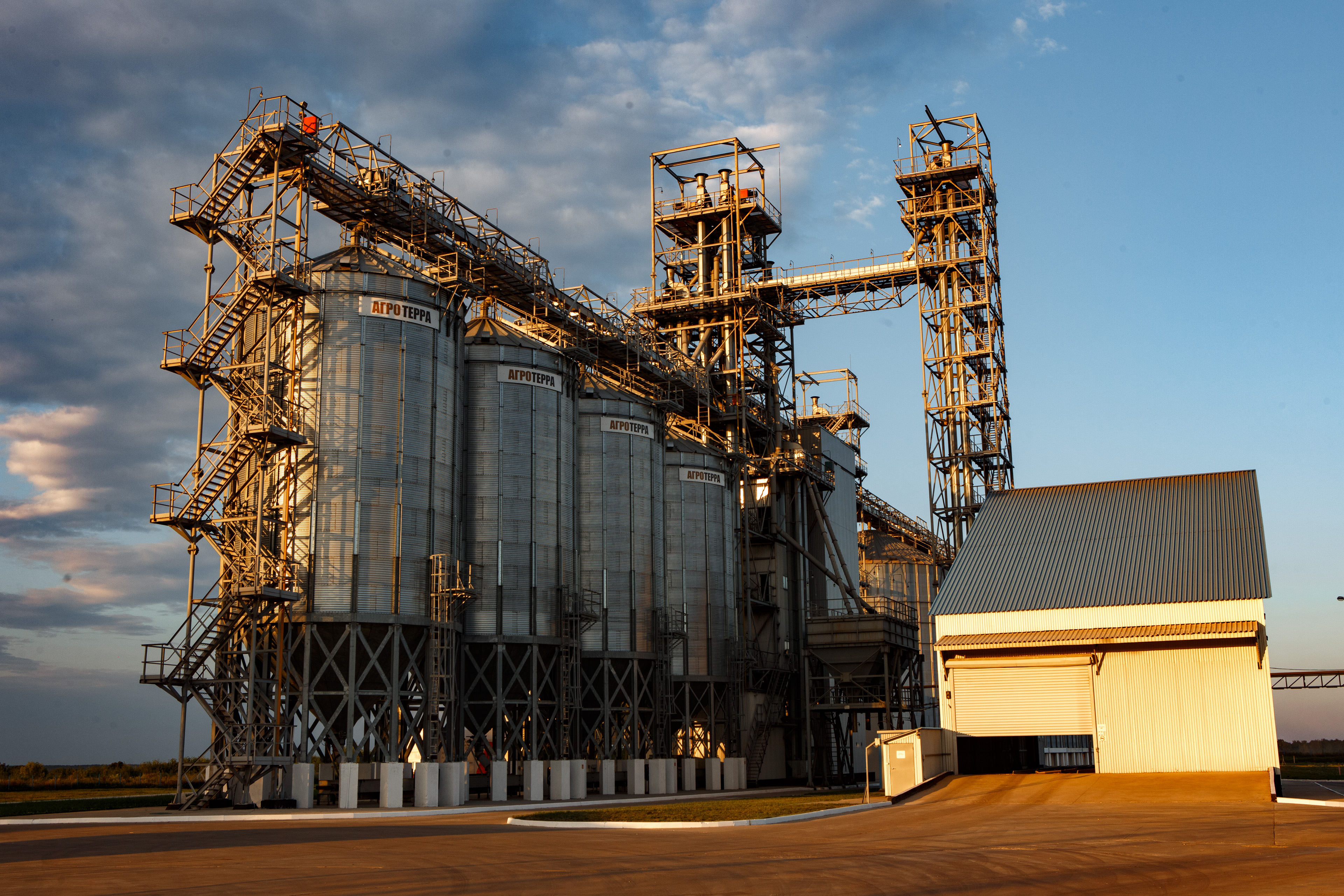
The AgroTerra Group carried out a point-by-point upgrade of process equipment at its elevators and updated internal grain transportation routes in Kursk region. The equipment can now be configured to accept and ship grain simultaneously, or to significantly increase the productivity of each process. According to preliminary estimates, efficiency has increased by approximately 20%. For the company, improving efficiency is an important factor, as AgroTerra is interested in a constant increase in the rate of return on invested capital.
In addition to equipment upgrades, cargo flow management processes have been updated. Elevators, logistics and production departments have agreed on future grain movements in a three-day planning format. Loading of the elevators has become more predictable. This allows more grain to be stored by partners. Acceptance itself is also performed faster: the peak hours are known and short. Thanks to the new approach, the speed of harvesting has increased and the need for hired freight vehicles has decreased.
Simply put, costs have been reduced and the business potential of the company's elevators has increased, explains Igor Petrov, Production Director at AgroTerra Elevators: ‘Previously, when we had to perform several different operations, we had to do it sequentially, at different times. As a result, it could take considerable time for just one batch of grain per thousand tons. Now, thanks to the fact that we can do some processes at the same time, we need less time. Accordingly, we are making better use of both the capacity of the elevator and the time of our employees’.
Product storage is one of the services that AgroTerra provides to its partners. The company has built the entire production cycle for agricultural producers: seed sales - agro-consultations - product storage - crop purchase.
The company will replicate its improvements in other regions.